Research and Development
Develop decarbonization and resource recycling technologies and contribute to a sustainable society.
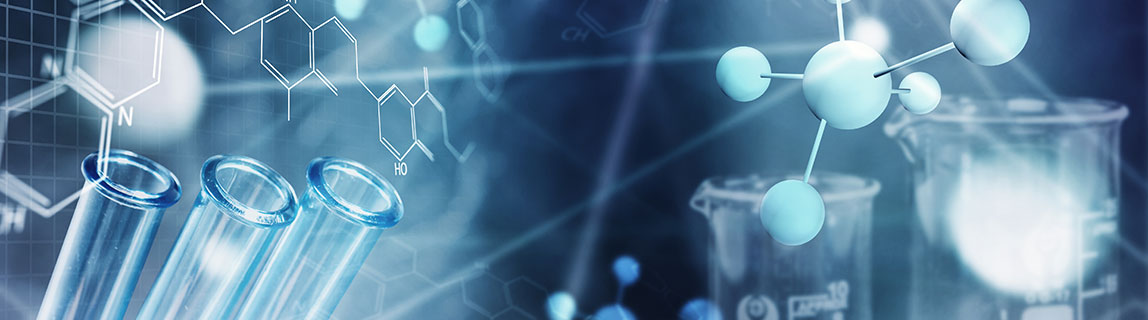
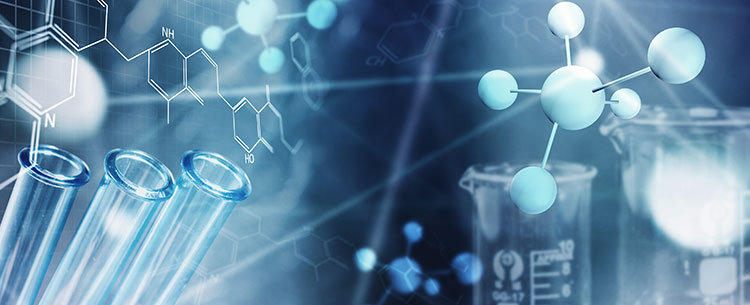
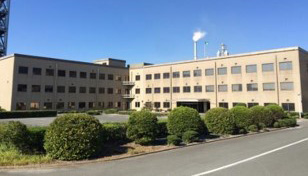
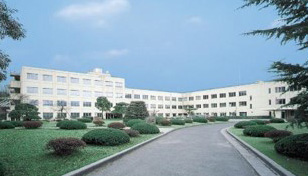
Using long years of knowledge accumulated in the cement research field, we develop high-performance cement, concrete and cement-based soil stabilizer satisfying diverse fluidity, strength, durability, ecofriendly and other needs. Furthermore, technology development regarding waste and byproduct utilization is also ongoing.
In addition, we accelerate the development of CO2 mitigation and utilization technologies towards carbon neutrality.
Our leading research skills continuously enhance our research foundation for the future.
Cement
In Japan, the cement industry has been playing a significant role in economic and social development for over 140 years by developing and providing basic materials for social infrastructure, such as buildings, dams, tunnels, bridges and so on.
Cement production can use resources containing CaO, SiO2, Al2O3 and Fe2O3 as raw materials, and the high temperatures between 1,400 and 1,500 °C detoxifies them safely. This feature enable us to utilize a large amount of waste and byproducts, which also contributes to a circular economy.
At the same time, the cement industry emits large amount of CO2, which is one of the greenhouse gasses, as a main raw material is limestone and a large amount of fuel is necessary to process it at high temperature in the production process. Therefore, we work on the development of CO2 capture and utilization technologies as well as energy saving towards the reduction of CO2 emissions.
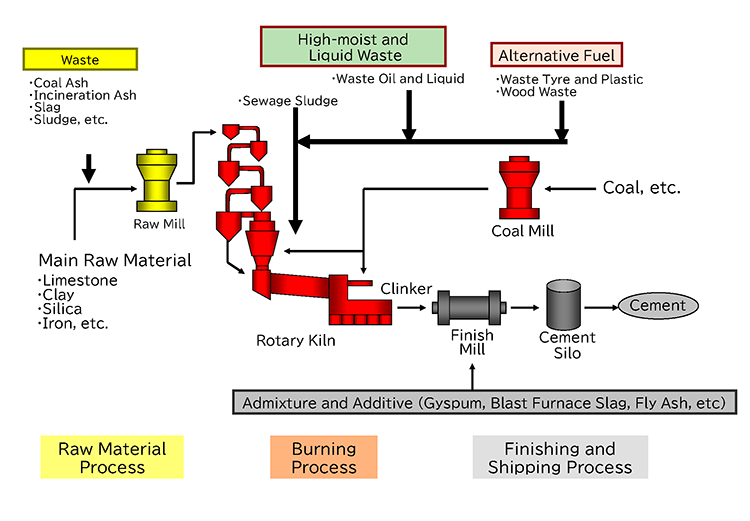
R&D Field
Our group-wide R&D covers extensive fields from construction materials exemplified by cement as a main business for social infrastructure to decarbonization, resource recycling and environmental improvement for a sustainable society.
Furthermore, we accumulate technology and knowhow to expand business fields including overseas activities, and strive for leading technology with a view of new business creation.
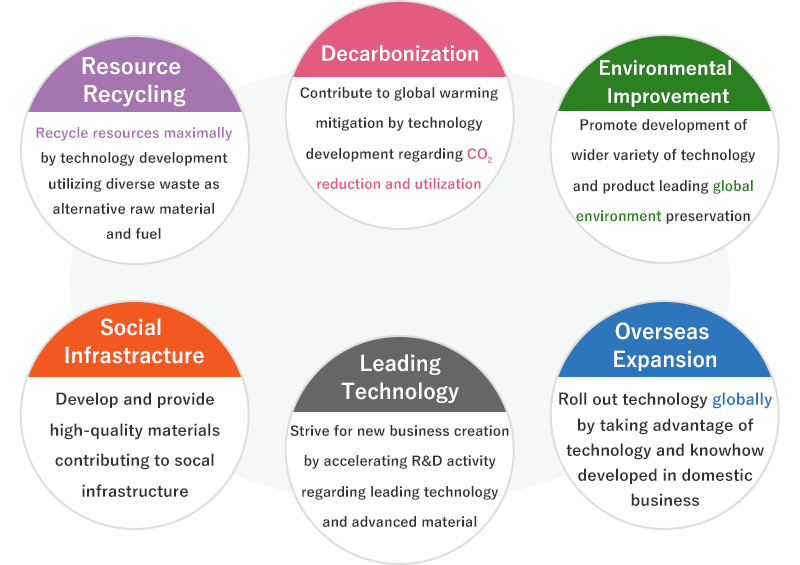
Action Towards Carbon Neutrality
We actively engage in development regarding CO2 capture and utilization technology and other technologies as part of global warming countermeasures towards the MUCC group's carbon neutrality goal.
CO2 Capture and Methanation Technology
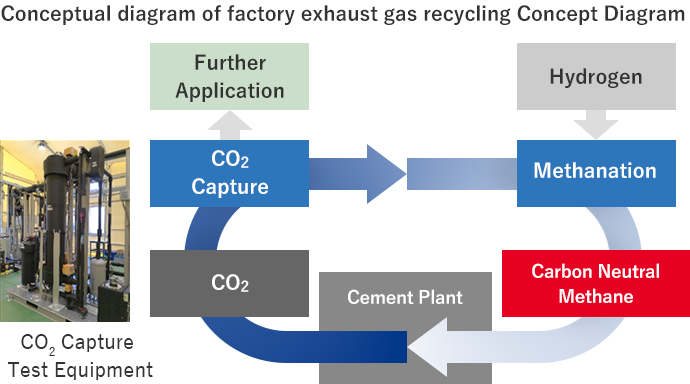
Fuel Conversion in Cement Production
(Use of synthetic methane)
Comprehensive demonstration is in progress, such as the demonstration of capturing CO2 from flue gases in cement plants, methanation by synthesizing CO2 and hydrogen, and the application of synthetic methane as a carbon neutral fuel.
CO2 Capture and Mineralization Technology
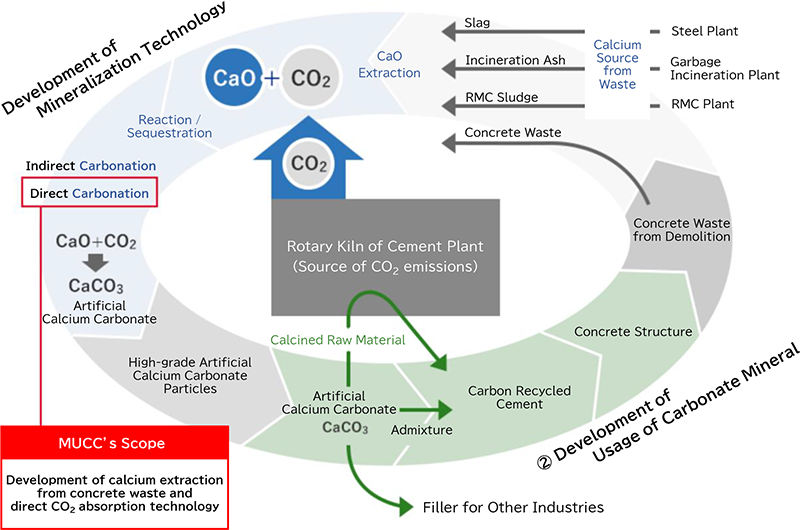
NEDO / Green Innovation Fund
Development of a cement production process with CO2 capture - Establishment of mineralization technology utilizing diverse calcium resources
- General Outline
-
Cement (whose main ingredient is CaO) is industrially produced through a CO2 separation process from natural limestone (CaCO3).
Another option is to extract CaO from a wider variety of waste containing calcium, such as concrete waste, incineration ash and others, have this waste react them with captured CO2 emitted from cement plants to generate artificial calcium carbonate (mineralization), and utilize them in cement production.
We aim for carbon neutrality in the cement industry by producing carbon recycled cement made from these raw materials.- 1Development of Mineralization Technology
We develop and verify different mineralization technologies, such as direct and indirect carbonation processes, to figure out a suitable one for a wider variety of waste containing calcium.
- 2Development of Use of Carbonate Minerals
This activity includes the verification of artificial calcium carbonate in uses as a raw material and admixture for producing carbon recycled cement, and the development of materials satisfying concrete performance needs (strength, etc).
We aim for deployment in the society by also preparing guidelines for design and construction.
Our scope in this project is to study the effective extraction of cement paste (CaO) from concrete waste and the direct carbonation (CaCO2 generation) of cement paste by using flue gas (CO2) in cement plants
- 1Development of Mineralization Technology
Fuel Conversion in Kiln (Ammonia Combustion)
We replace fossil fuels used in rotary kiln burners with ammonia to establish fossil fuel derived CO2 reduction technology.
- *Cabinet Office’s SIP project (2014-2018) for the technology development of ammonia co-combustion cement kiln, Ube Industries Ltd. (currently Mitsubishi UBE Cement Corporation) and Osaka University
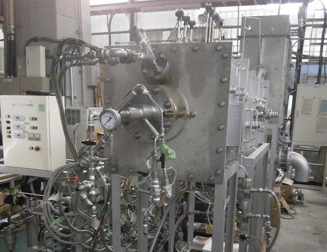
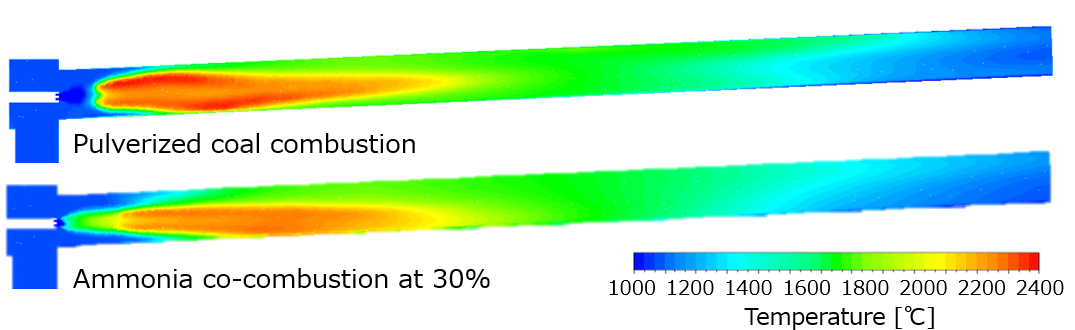
Contribution to a Circular Economy
We contribute to a circular economy through the development of recycling technologies utilizing a wider variety of waste.
The following are examples of the developed recycling technologies.
Sewage Sludge Fermentation and Drying Technology
Technology Concept
- Before : Drying technology (Heat drying using fuel)
-
- Large amount of fuel-derived GHG emissions.
- Easily biodegradable organic matter remained in dried sludge requires careful handling as fertilizer.
- Before : Composting technology (compost depot, mixing)
-
- Processing time is from 30 to 100 days.
- Experience is necessary for operations.
- Odor control measures are challenging.
- Main Technology
-
Plasterboard Waste Recycling
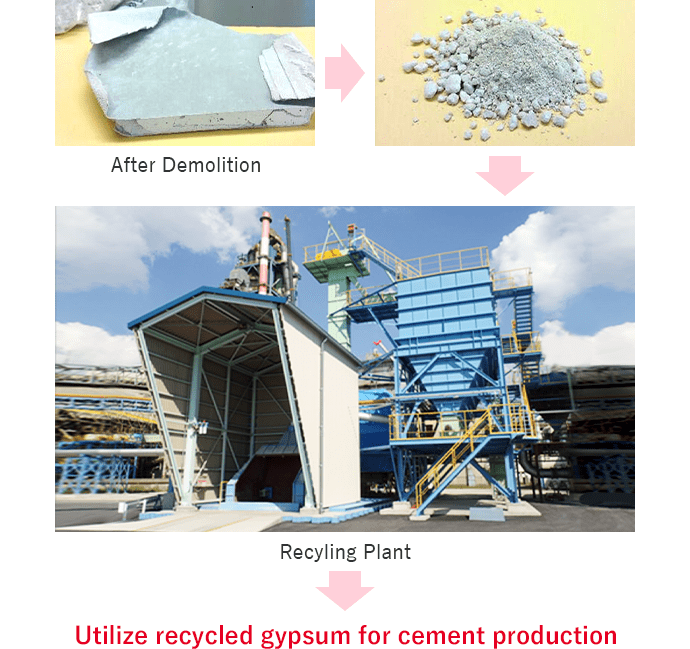
Development and Commercialization of Environmental Contribution Products
We develop environmental contribution products towards the improvement of the environment and preservation of nature.
Cement-based Soil Stabilizer
We gather basic data on the characteristics of improved soil, then develop and improve cement-based soil stabilizer for soft soil nationwidee soft soil.
Cement-based soil stabilizer areis designed to effectively form hydration products (ettringite, calcium silicate hydrate) and achieve superior solidification performance according to the type of soft soil.
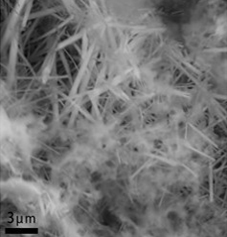
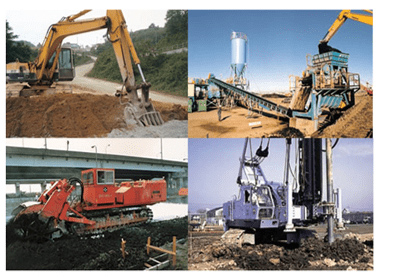
Heavy Metal Immobilization Materials
We provide environmental improvement materials for soil, air and water.
In the field of soil improvement, R&D activities for heavy metal immobilization materials and neutral solidifying materials mainly containing magnesium oxide are in progress.
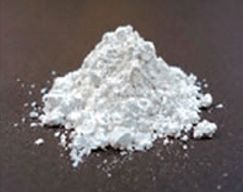
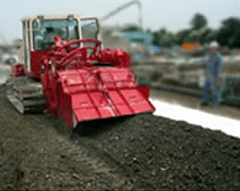
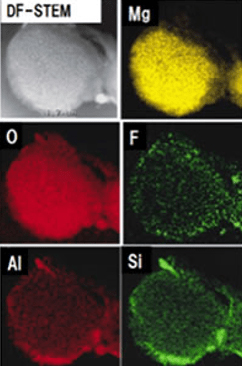
High-Performance Product for Social Infrastructure
We develop high-performance construction materials to accommodate social needs.
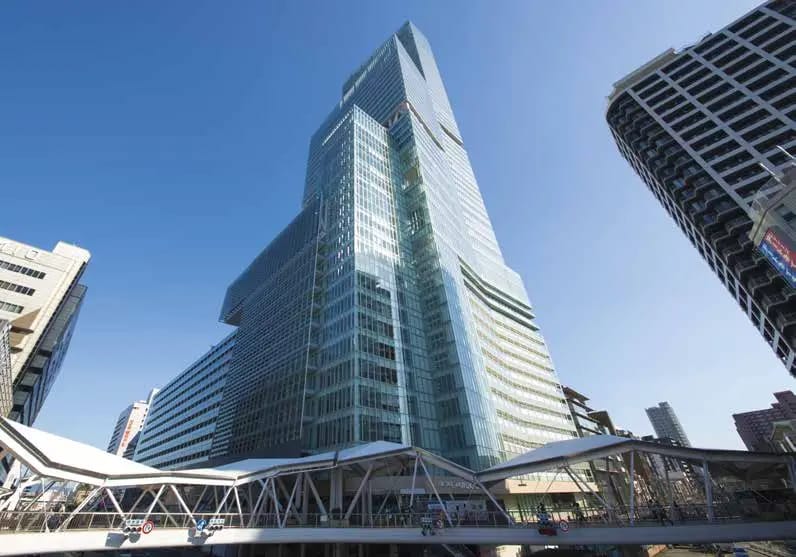
High Strength Cement
Product Name: Silica Fume Cement
Silica fume cement is designed to meet requirements for high strength and fluidity by adding ultrafine particles of silica fume to low heat Portland cement.
This product is used for a wider variety of structures because of the high strength and fluidity performance required for high strength mass concrete structures, reinforced concrete skyscrapers, concrete- filled steel tube structures and others.
Admixture for High Strength Fiber Reinforced Concrete
Product Name: Sitehard
Sitehard is special material for ultra-high strength fiber reinforced concrete with curing properties at ambient temperature.
This product is developed by taking advantage of special cement production technology and a concrete mix design technique.
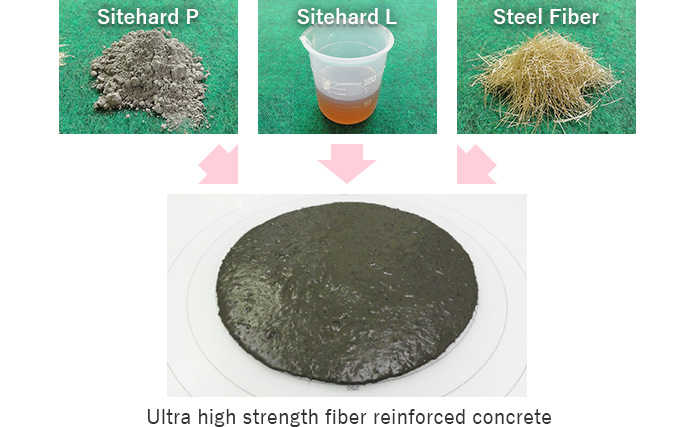
Special Admixture for Salt Resistant Concrete
Product Name: Chloroguard
Chloroguard is special admixture enhancing the salt resistance of concrete by replacing a part of cement.
This product is developed by taking advantage of concrete mix design technique and performance assessment experience, contributing to the improvement of durability and the product lifetime of concrete structures.
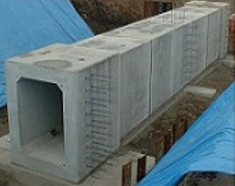
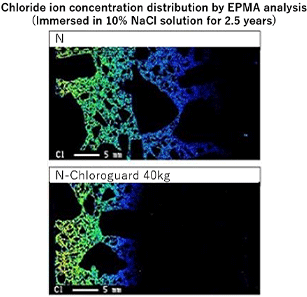
Leading Technology and Basic Research
We continuously work on the development of simulation technologies and basic research for new applications of cementitious material for further technology development.
Development of Simulation Technology
We are a leading company in the development of simulation technology (integrated simulator) for cement production processes.
By upgrading this simulation technology, it will be useful for not only contributing to the stable operation of cement plants utilizing waste but also design optimization in the field of energy conversion and CO2 capture processes towards carbon neutrality.
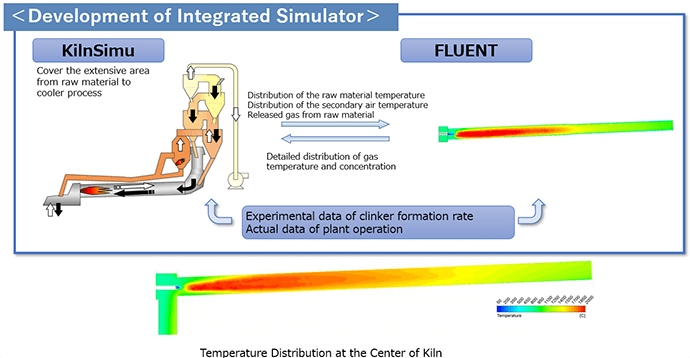
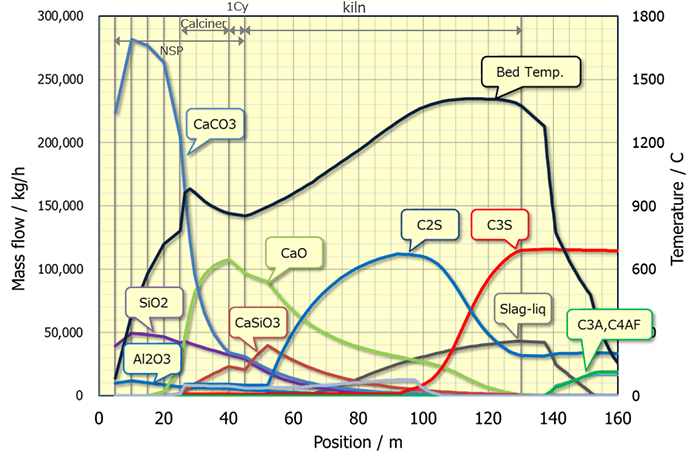
Cement-Based Material Use in the Deep Sea
The deep sea is a highly attractive field in terms of the development of new mineral resources such as rare metals.
We strive for material development with a view of the future demand for structure construction in the deep sea by considering the progress regarding the active exploration of marine resources surrounding Japan.
We conducted a durability study of cement-based materials under deep sea conditions for the first time in the world.
This revealed information about special cement mix design and mechanical damage under the high-pressure water conditions in the deep sea.
In 2022, we succeeded in a basic experiment using an actual cement-based material in deep sea.
These research results were published and highly evaluated internationally.
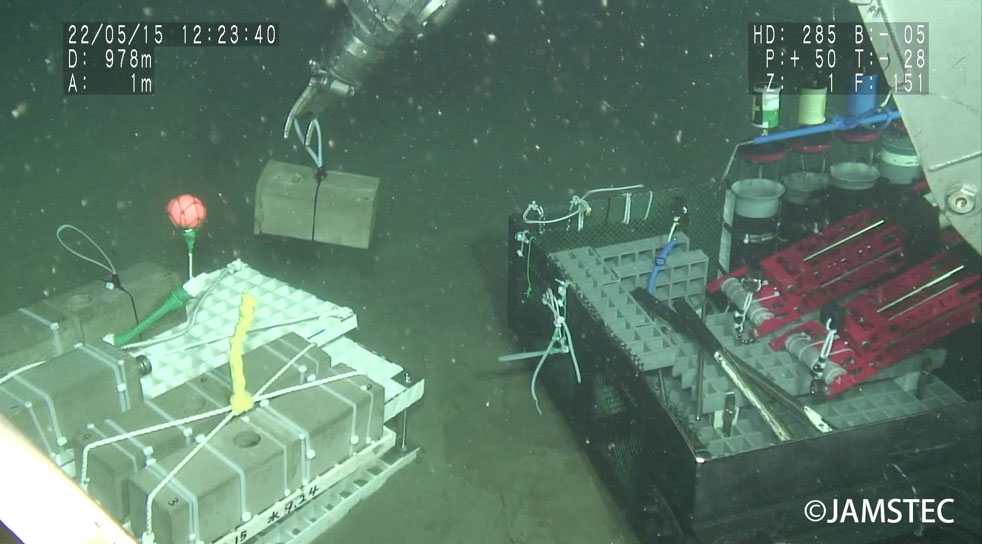
- Research Result
-
- Mari Kobayashi, Keisuke Takahashi, Yuichiro Kawabata, Physicochemical properties of the Portland cement-based mortar exposed to deep seafloor conditions at a depth of 1680 m, Cement and Concrete Research 142 (2021) 106335
- Mari Kobayashi, Keisuke Takahashi, Yuichiro Kawabata, Thomas Bier, Physicochemical properties of Portland cement/calcium aluminate cement/calcium sulfate ternary binder exposed to long-term deep-sea conditions, Materials and Structures 55 (2022) 182
- Keisuke Takahashi, Yuichiro Kawabata, Mari Kobayashi et al., Action of hydraulic pressure on Portland cement mortars – Current understanding and related progress of the first-ever in-situ deep sea test at a 3515 m depth, Journal of Advanced Concrete Technology 19 (2021) 226–239
- Keisuke Takahashi, Yuichiro Kawabata, Mari Kobayashi et al., In-situ deep-sea monitoring of cement mortar specimen at a depth of 3515 m and change in mechanical properties after exposure to deep sea condition, Journal of Advanced Concrete Technology 20 (2022) 254–266